Automated ICJs and Binders
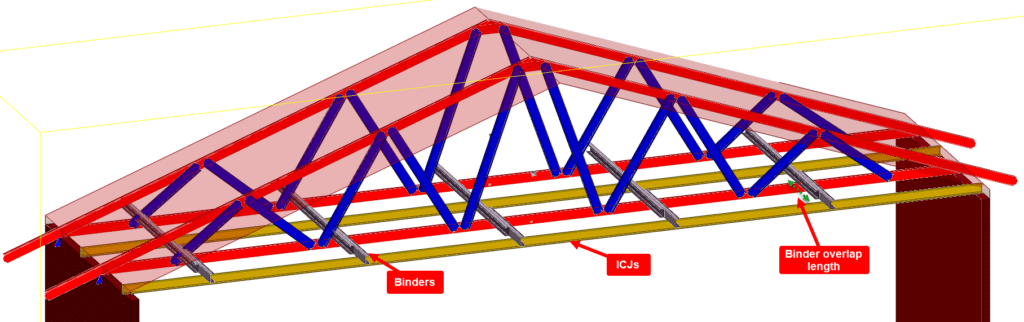
A Smarter Way to Design Light Gauge Steel Roof Structures
At Enduroframe, we’re always looking for ways to make roof design more efficient, precise, and user-friendly. That’s why we’re excited to highlight a powerful enhancement in our software: Automated Intermediate Ceiling Joists (ICJs) and Binders. This feature streamlines ICJ insertion, making it easier than ever to reinforce ceilings while reducing manual effort.
What Are ICJs and Binders?
ICJs are structural members that run parallel between trusses, at the same height as truss bottom chords. They provide key support for plasterboard ceilings and eliminate the need for ceiling battens or running trusses at closer spacings. In cases where trusses are spaced at 1200mm, ICJs help can provide a working platform when working at height.
Binders, on the other hand, run perpendicular to trusses and ICJs, sitting above roof truss bottom chords. They support the ICJs, ensuring a stable and well-distributed load. Binders can also be used as lateral restraints for truss bottom chords.
ENDUROCADD® Automation
Previously, adding ICJs and binders was a very manual process, requiring detailers to add members one-by-one as beams. Now our automated ICJ and binder insertion takes the guesswork out of the process. The ENDUROCADD® software follows built-in design rules to automatically place ICJs and binders where needed, ensuring optimal structural integrity. Users can also fine-tune settings for complete customization.
Key Features & Benefits
✅ Automatic ICJ Placement – ICJs are intelligently inserted at the midpoint between roof trusses, ensuring proper support and reducing manual input.
✅ Flexible User Configurations – Choose the section type, truss spacing, maximum ICJ length before splicing, and whether to add ICJs across the entire roof or block by block.
✅ Smart Binder Integration – Binders are placed at user-defined spacing, supporting ICJs seamlessly. Users can define overlap lengths and choose whether binders are boxed.
✅ Precision Manufacturing Data – ICJs and binders are now included in the BOM (Bill of Materials) and NC data for seamless manufacturing and job tracking in ENDUROCADD NX and ENDUROHUB.
Why It Matters
Eliminating repetitive tasks makes life easier for detailers. Automating ICJs and Binder insertion in ENDUROCADD® software is just one example of our ongoing commitment to innovation and continuous improvement of the ENDUROFRAME® building system.
For installers, it can mean less trusses and/or ceiling battens to install while providing a safe work platform, making a cost-effective roof solution!
Find out how to start making frames
With automated ICJs and binders, we’re making Light Gauge Steel roof detailing more efficient, accurate, and customizable than ever.
Contact Enduroframe