Solutions to Fix Anything to LGS Wall Frames
A common question is how to fix pictures, shelves and other items to LGS walls. This article explains the solutions available with the ENDUROFRAME® building system.
Attaching pictures, brackets, towel rails and shelves to steel frames is a common query we receive for ENDUROFRAME® building system support. Here’s how you can do it effectively:
For hanging pictures, use readily available hooks from any hardware store that attach directly to the plaster. This method doesn’t require a stud and can support up to 20 kg.
To attach directly to a stud, simply use a coarse thread self-drilling or self-tapping screw through a predrilled hole.
For a more secure fix for heavy items like TVs, cupboards, and towel rails, our ENDUROFRAME® building system includes a unique face fix nogging solution. This feature, added during the detailing stage of new homes, ensures a robust mount that won’t fail, providing long-term value and peace of mind.
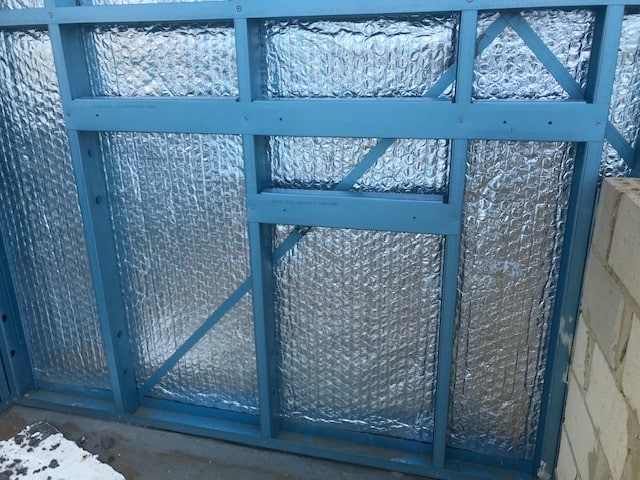
Find out more
Contact our team to find out how to start making efficient light gauge steel frames, or contact one of our experienced licencees who manufacture the ENDUROFRAME®️ building system
Contact Enduroframe todayFind a supplier