How sophisticated testing and engineering leads to cost-effective light gauge steel trusses
A common misconception is that all light gauge steel roof trusses spanning the same distance and with the same loads use the same amount of steel. This is not true. Smart research and development in trusses and sophisticated software can provide reductions in steel usage of up to 50% compared to less efficient light gauge steel trusses.
The ENDUROCADD® design software has been developed over 20 years as a design tool for the ENDUROTRUSS® system, a key component of the ENDUROFRAME® building system. Over this period the system has responded to changes in building construction, design standards and regulatory requirements.
The foundation of this success is a commitment to extensive testing of truss connections and entire roof truss assemblies at our state-of-the-art NATA-accredited laboratory in western Sydney. All truss connections are tested in compliance with AS4600: Cold formed steel structures. Once the results have been verified the data is fed into our ENDUROCADD® software to provide efficient steel truss designs.
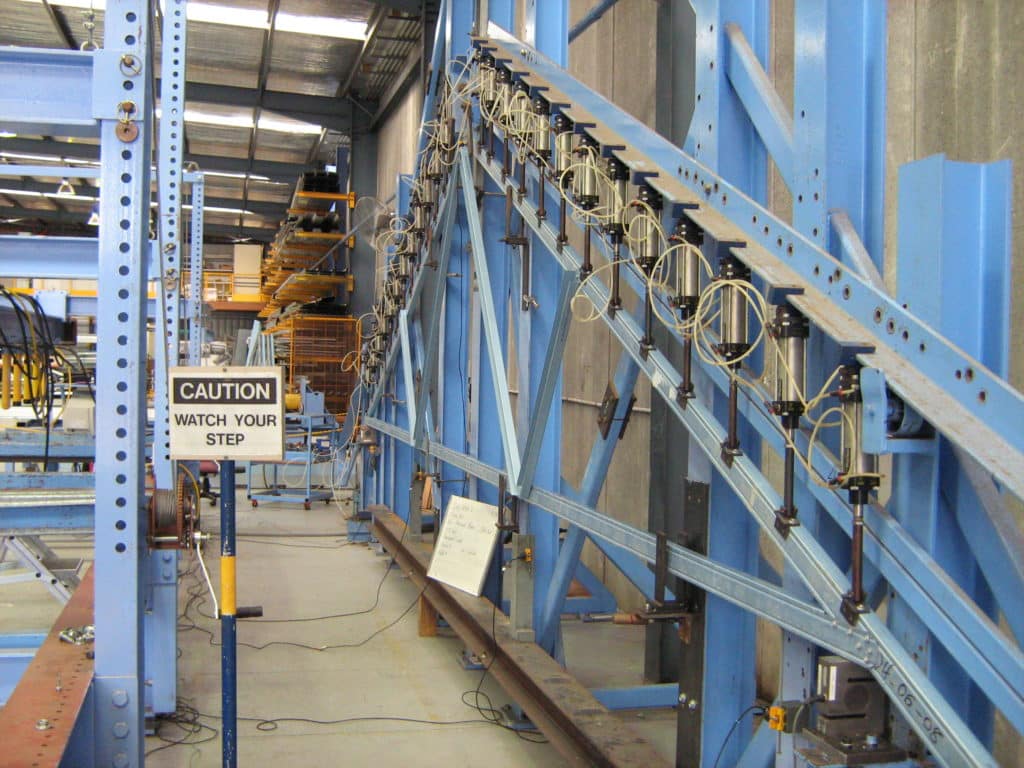
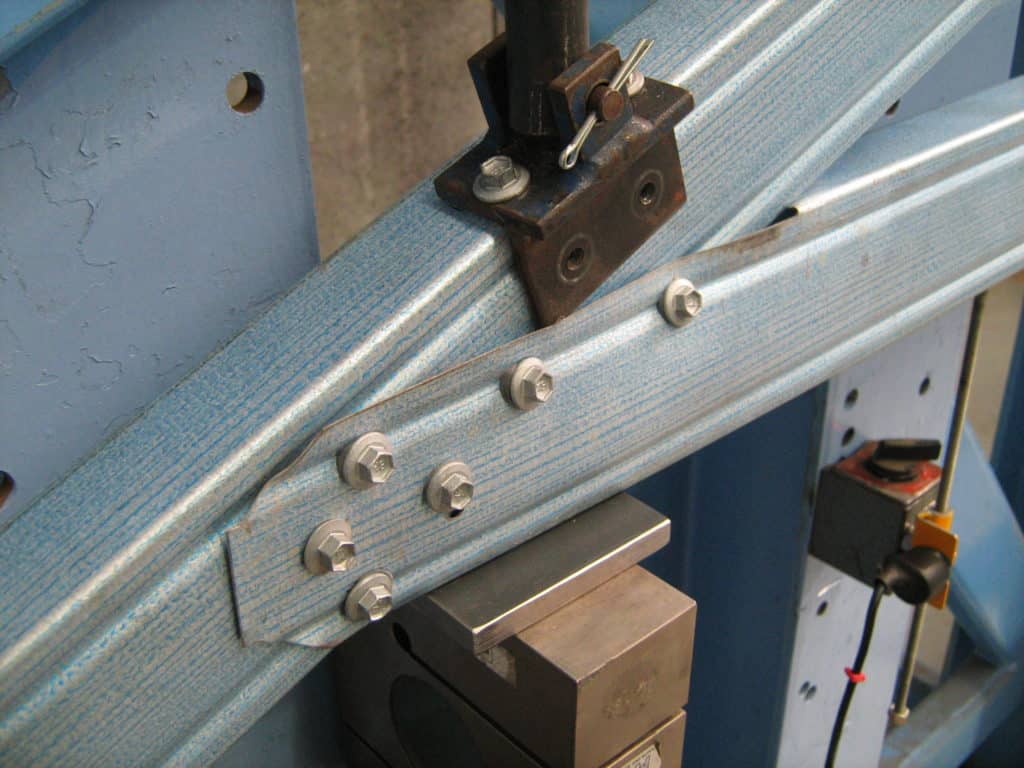
Putting our testing to the test
We are so confident in our testing that a decade ago we put forward the ENDUROCADD® software to be used as a test case for the drafting of the ABCB Protocol for Structural Software. This was a huge deal for our customers because under this Protocol, trained software users of compliant software applications are permitted to design and sign-off buildings that fall within the Protocol scope. Compliance with the ABCB Protocol for Structural Software means expensive and time-consuming engineering approvals can be avoided
The ABCB Protocol for Structural Software requires independent verification from a third party to ensure that software calculations comply with the Building Code of Australia (BCA) and Australian design standards. Swinburne University provides independently checks that the ENDUROCADD® software complies with the Protocol.
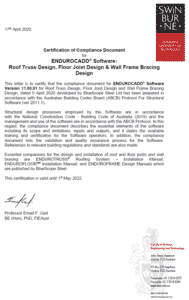
Working with the benefits of extensive testing
When you use the ENDUROCADD® software, you are presented with intuitive truss design functions that test every load case defined in the loading standards. The ENDUROCADD® software runs design and analysis for all members and connections which, in a typical truss, will be 112 load cases. This ensures that all required load conditions are considered and provides confidence that trusses are structurally sound.
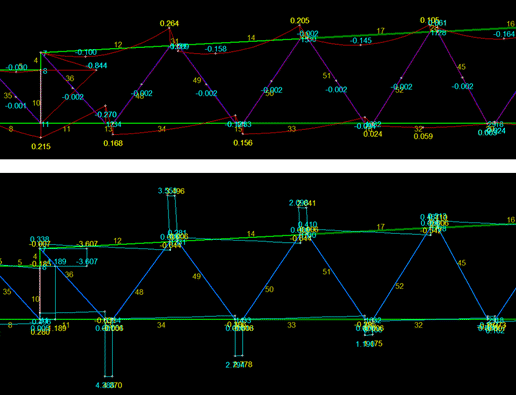
When your job is complete, you can view detailed connection drawings that show required screw types and their installation locations. Even better, when truss components are produced the number of screws required at each chord-to-web and chord-to-chord connection is inkjet marked on the parts. This avoids any confusion during assembly.
There are many connection options which include multiples of screws and different types of gusset plates to vary the connection capacity. As there are about 2000 different connections, a summary sheet of the connections required for a specific job are generated for easy truss assembly.
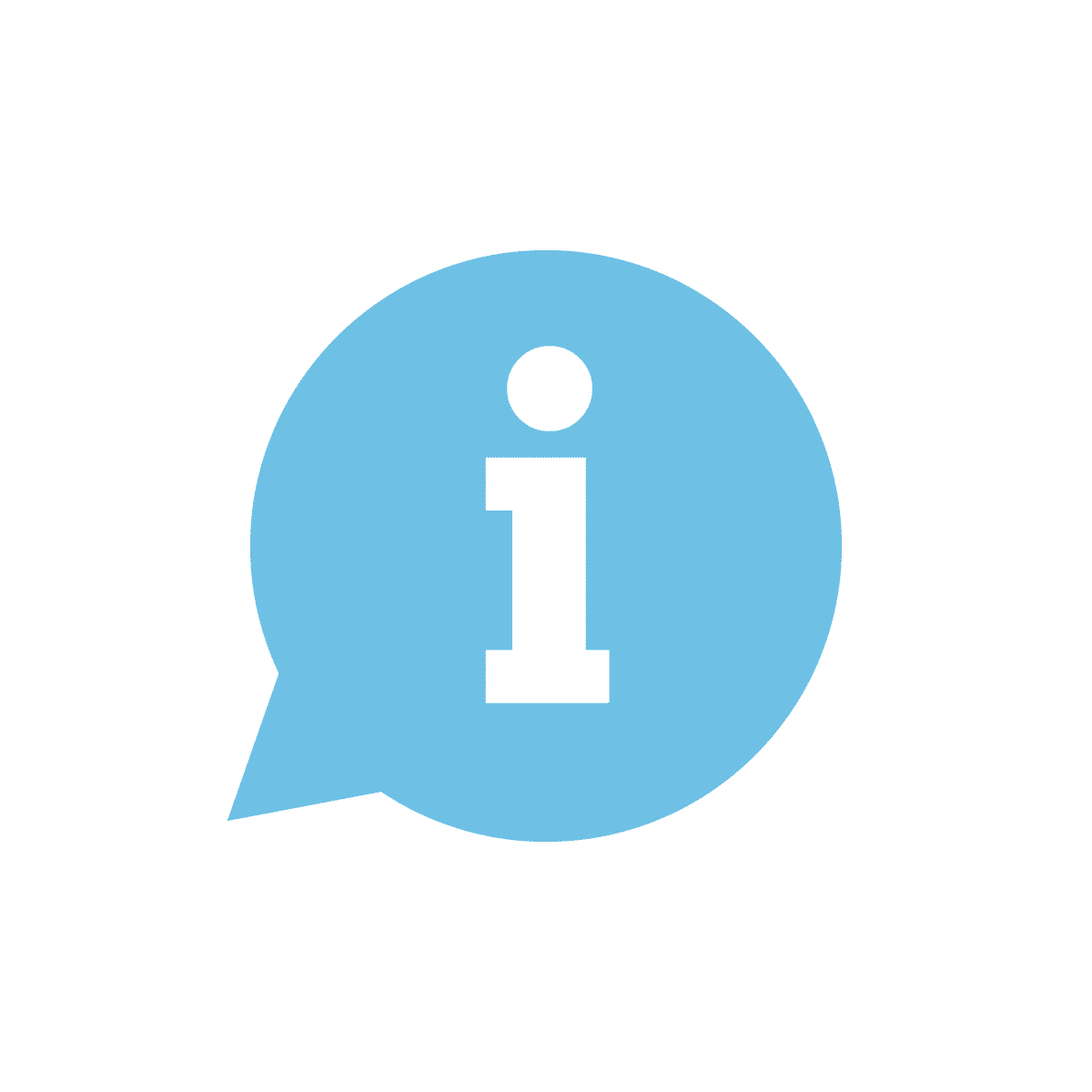
We believe the number of truss connections is the most of any light gauge steel framing system. This reduces the chance that connections are the determining factor in the truss strength and performance. In turn, this increases the cost effectiveness of the truss system. It is always cheaper to increase the capacity of a connection with a few screws than it is to increase the gauge of steel used in the entire roof truss.
Boxing Saving Costs

Boxing is another way the ENDUROCADD® software helps you reinforce truss chords and webs just where additional strength is required without increasing the overall truss gauge. Boxing is inserted on the reverse side of the truss to the webs and is precisely positioned where required to resist loads. In the diagram above, the darker section demonstrates the sections of truss chords that are boxed. In many cases chord boxing does not need to extend along the entire length of the chord. The boxing part is manufactured together with the truss and, unlike in-plane trusses, the boxing can extend across multiple sections of chords and webs. Pre-punched holes assist with the location of boxing on truss chords.
We’ve created a set of posters showing the assembly details for roof trusses. Sticking these up in your factory is a great way to keep everyone on the same page. See ENDUROTRUSS® fabrication posters.
Find out more about how the ENDUROFRAME® system reduces truss costs here.
For drawings and photographs that clarify truss construction, please read the ENDUROTRUSS® installation manual. See ENDUROTRUSS® Roofing System Installation manual.